PPE Model for achieving safety excellence
People, Process, and Equipment is a research-based model developed by CLIDE to improve the safety maturity level of an organization.
PPE Model
People, Process and Equipment helps organization improve the safety maturity curve. The model helps identify the enablers and barriers related to three major pillars of the organization and those are - People who perform the activity, Process - which are designed for safe work and Equipment - which are used to process the raw material to finished goods.
The gap in any of the three pillars or all indicates the improvement scope for management and in order to achieve operational excellence. Organizations should adopt a data-driven decision-making model to achieve sustainable safety culture.
PPE Mode
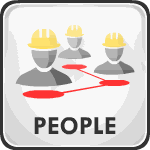
People
People safety indicator is nothing but the expected behaviour in the organisation. If workforce shows the expected behaviour while executing the work, than you achieve “ People Excellence ”
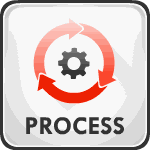
Process
Process Compliance indicator is all about established practices guided by well defined SMS standards to achieve zero deviation for maturity alignment with safety needs.
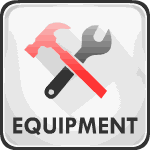
Equipment
Risk based Equipment periodic maintenance will have greater life cycle and reduced failure rate. Productivity enhancement is a good indicator for Equipment Excellence .
PPE Model
CLIDE PPE Model can be implemented at any stage on the safety maturity model and help you achieve SMART goals. With the help of formulating “Internal Safety Improvement Team” which acts as a prime mover to shape the culture by developing leaders, through coaching & training, and monitoring the leading indicators.
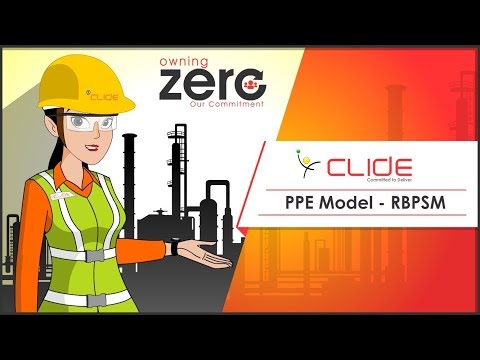
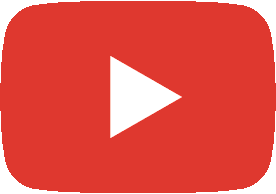
Pillar 1 - People
Expected Behaviour
The expected behavior is the first element in People. Every organization should design the expected behavior list and communicate the same to the workforce.
Training & Education
Training and Education is the second element in People. Training and Education should be given to the workforce as a part of the continuous improvement process. Training should be considered as an investment.
Performance Indicators
Performance Indicators are the third element in People. Leading and lagging indicators should be designed as per the process of the organization. Periodic reviews should be taken to take corrective action in safety improvement.
Safety Culture
Safety Culture is the fourth element in People. A safety perception survey should be done so as to know what the workforce thinks about safety in the organization.
Employee Involvement
Employee Involvement is the fifth element in People. Employee involvement should be encouraged to achieve people's excellence towards safety.
Pillar 2 - Process
Operating Procedure
A standard operating procedure (SOP) is a set of step-by-step instructions compiled by an organization to help workers carry out routine operations safely.
HIRA-RC
Hazard Identification Risk Assessment (HIRA) and control measure should be well defined for a activity. Implementation of the same at organisational level define the safe workplace.
Safety Audit
Safety Audit carried out in organization to know the level of compliance as per the organization processes. How organization also check the beyond compliance level to make the workplace more safer.
Review Mechanism
Comprehensive review mechanism will be of highest importance for the implementation of gap identified in the processes. Reviewing helps know progress of actual vs standard.
GMP
Implementation of good manufacturing practices helps to benchmark the processes help organization reduce the process risk and have safe work procedure.
Pillar 3 - Equipment
Periodic Inspection
Periodic inspection of equipment helps organization know the health condition and reduce the hazard and risk associated with equipment failure
PSSR
Carrying out Pre-start up review after a shutdown of equipment for a period of time helps start the operation safely reducing the chance of any failure.
S & Q - Assurance
Having a strong safety and quality assurance plan in place helps management know
that organisational arrangements and processes for safety achievement are properly applied and continue to achieve their intended objectives
Equip- Performance
EP is one of the measures indicating how well a manufacturing operation is utilized: Overall Equipment Effectiveness, or measures the percentage of scheduled production time that is fully productive.
Engineering Control
Engineering controls protect workers by removing hazardous conditions or by placing a barrier between the worker and the hazard. The percentage of equipment safety can reduce the chance of any incident.
CLIDE Safety Excellence Model
CLIDE Safety Excellence Model covers people, procedures, and equipment. If all three elements are implemented in the organization, operational excellence can be achieved which leads to business excellence.
Operational Disciple
OD is defined as dedication and commitment towards the job one performs.
PPE Pillars
People, Process and Equipment are the core to achieve Safety Excellence in the organization.
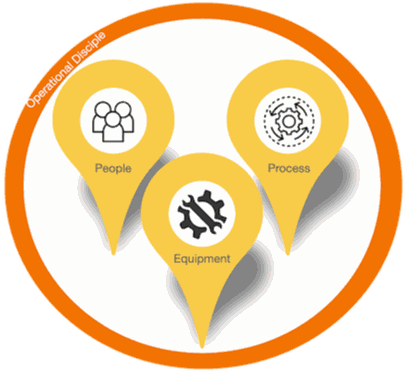
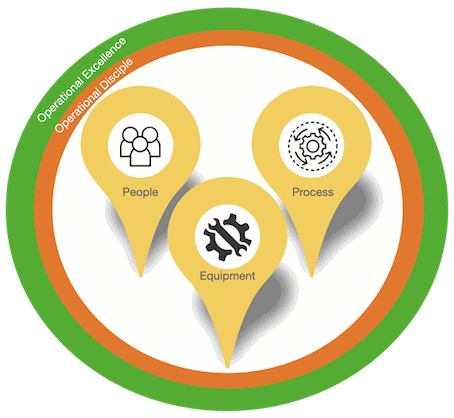
Safety Excellence is to recognize employee
excellence
in both action and attitude that is consistent with advancing safety needed as per business core values.
Operational Discipline - OD
OD is defined as dedication and commitment towards the job one performs
Operational Excellence - OE
OE is the systematic management of safety, health, environment, reliability and efficiency to achieve top performance
Talk to our consultant to know more about PPE Model
Join us and make your company a safer place.