Successful Implementation of Behavior-Based Safety (BBS) in the Steel Industry
In the complex and high-risk environment of the steel industry, safety is a critical concern. Our client, a leading steel manufacturer, sought to enhance workplace safety through the implementation of a Behavior-Based Safety (BBS) program. With over 5,000 employees working across multiple sites, the primary goal was to reduce incident rates and create a sustainable safety culture by targeting unsafe behaviors.
This case study outlines the structured approach taken to implement BBS over 2.5 years. It provides a detailed account of each phase, highlights the data-driven decisions made, and showcases the impact of the project using statistical insights.
Client Industry
Steel Manufacturing
Project Duration
2.5 Years
Consultant Involved
6 (Total Consultant)
BBS Consulting Project Phases and Approach
Phase 1 - Gap Assessment (First 3 months)
Before implementing any safety interventions, we conducted a thorough gap analysis . This step involved:
- Site Visits: Detailed inspections across multiple steel plants.
- Behavioral Observations: Conducting over 1,000 behavior-based observations.
- Incident Data Review: Historical data analysis of past safety incidents and near misses.
- Employee Interviews: Engaging with employees at all levels to understand perceptions of safety practices.
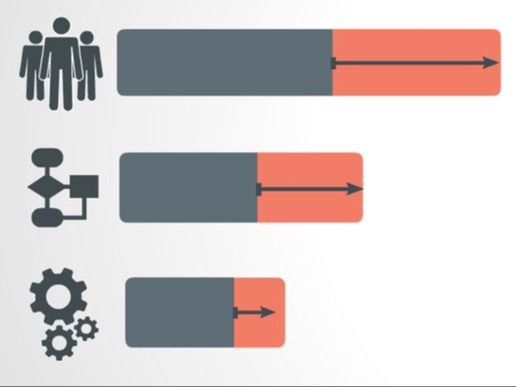
Phase 1 - Key Findings
Safety Procedure
Lack of consistent safety practices across different shifts.
Safety Culture
A reactive rather than proactive approach to handling safety incidents.
Employee Engagement
Minimal employee engagement in safety improvement initiatives.
Statistical Highlight: Phase 1
70% of the safety incidents were attributed to behavioral causes rather than equipment failures.
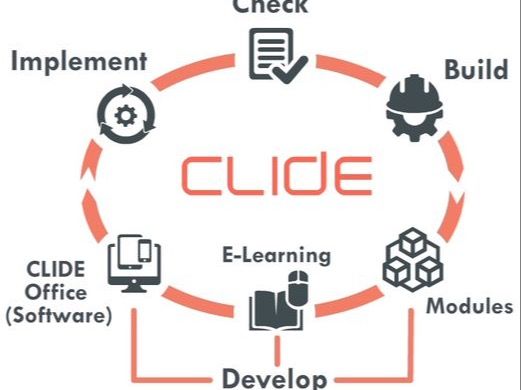
Phase 2 - Framing the Strategy (Months 4-8)
Post-gap assessment, we designed a customized BBS strategy tailored to the client’s operations. Key components included:
- Leadership Engagement: Ensuring commitment from top management.
- BBS Steering Committee Formation: Cross-functional teams to drive the BBS agenda.
- Action Plan Development: Specific goals to reduce behavioral risks in high-incident areas.
Data Driven Decision : Phase 2
The focus was placed on high-incident zones like the furnace and rolling mill, where 80% of unsafe behaviors were reported.
Phase 3 - Training & Communication (Months 9-14)
For successful BBS implementation, training was essential. This phase included:
- BBS Workshops for Leaders: Focused on leadership’s role in driving behavioral change.
- On-the-Job Training: Frontline workers were trained to identify unsafe behaviors.
- Safety Communication Channels: Digital tools and dashboards were set up for reporting and monitoring behaviors in real-time.
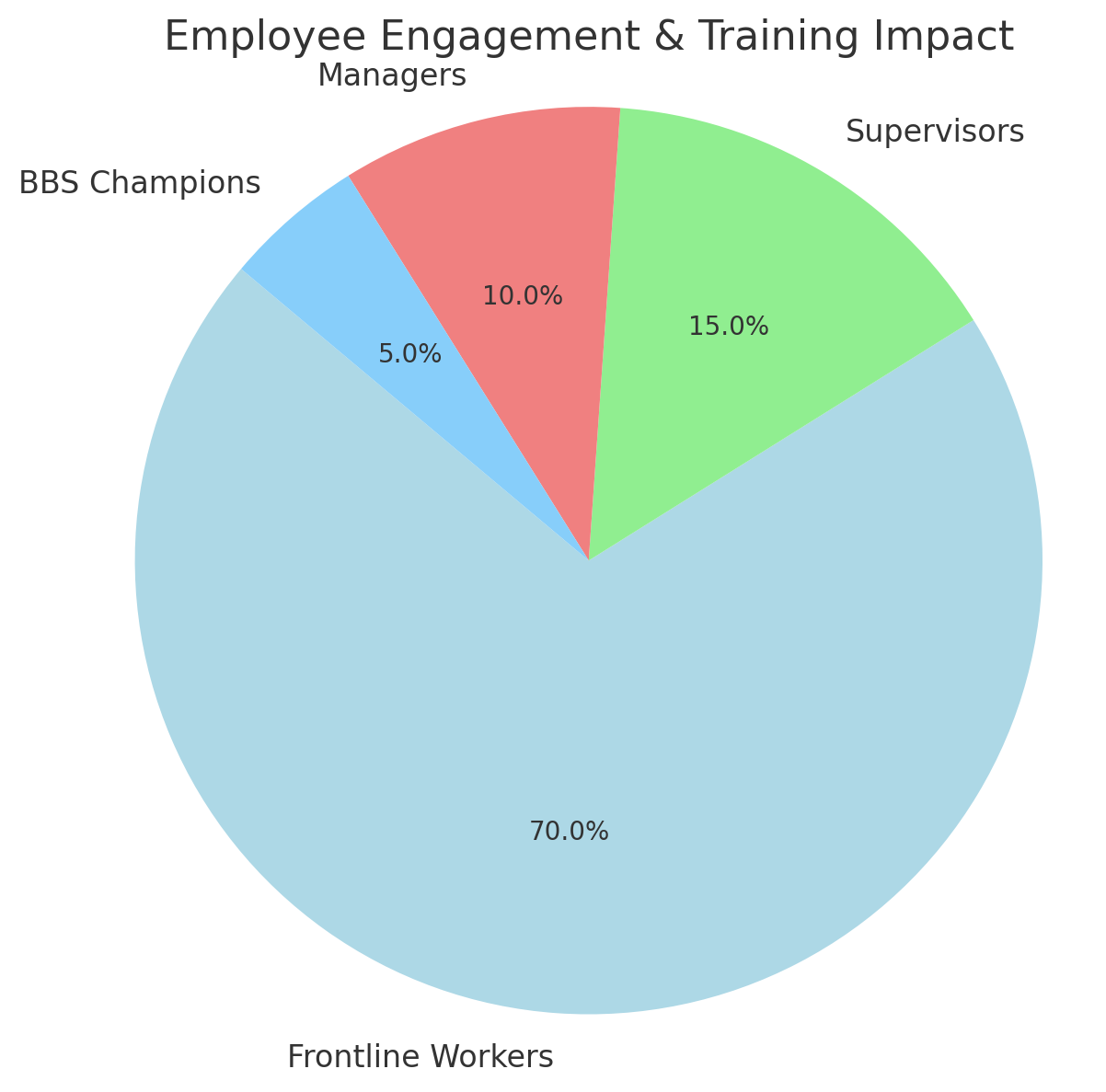
Phase 3 - Key Results
BBS Training
Over 2,000 employees were trained in behavioral observation.
BBS App
A 45% increase in safety reporting after the introduction of new communication tools.
Employee Engagement
63% participation increase in safety activities by frontline workers
Statistical Highlight: Phase 3
90% of trained employees reported feeling more confident in identifying unsafe behaviors.
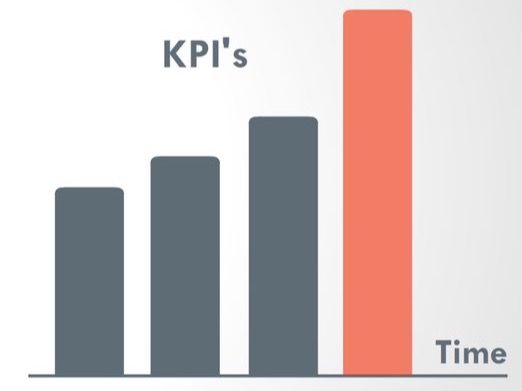
Phase 4 - Handholding & Implementation Support (Months 15-22)
During this phase, we provided on-site support to ensure the smooth execution of the BBS program:
- On-site Consultants: Six consultants were deployed to guide the BBS process.
- Mentorship Programs: Key employees were identified as BBS champions, who were mentored to sustain the program independently.
- Safety Observations: 50,000 safety observations were conducted across different shifts, with corrective actions implemented.
Data Driven Decision : Phase 4
Shift timings were restructured based on safety data, resulting in a 30% reduction in incidents during the night shift.
Phase 5 - Review Meetings & Continuous Improvement (Months 23-30)
Regular review meetings were integral to tracking the progress of the BBS program:
- Monthly Review Sessions: Discussing observation data, incident reports, and improvements.
- Behavioral Trends Analysis: Using analytics tools to assess patterns in unsafe behaviors.
- Employee Feedback Surveys: Regular surveys to gauge the program’s effectiveness.
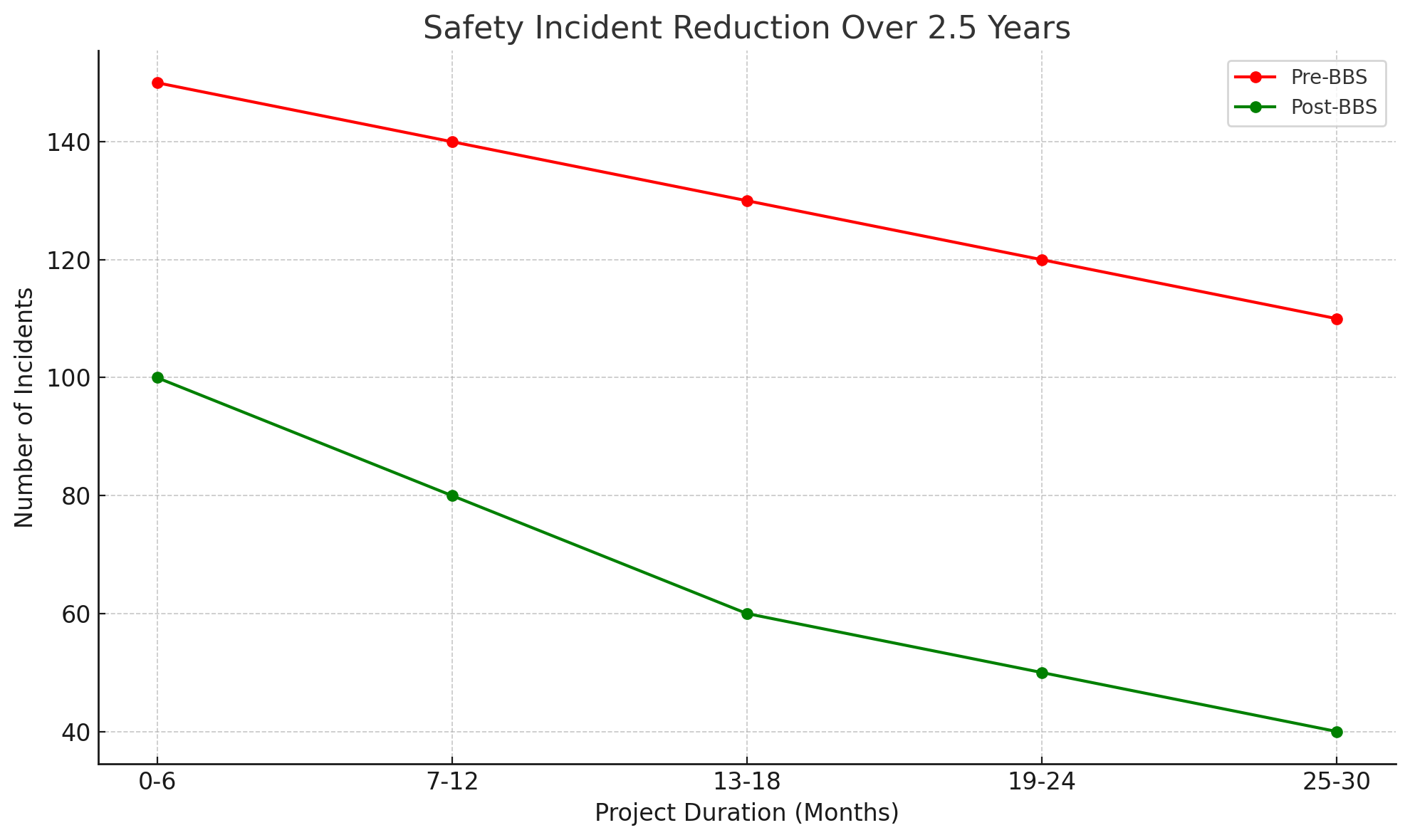
Phase 5 - Key Impact
Incident Rate
A 60% reduction in overall safety incidents at the workplace.
Compliance Rate
Consistent 98% compliance with safety protocols across all departments.
Behaviour Change
73% Increase in safe behaviour at the workplace across all department
Statistical Highlight: Phase 5
Post-BBS implementation, near-miss reporting increased by 200%, indicating heightened awareness.
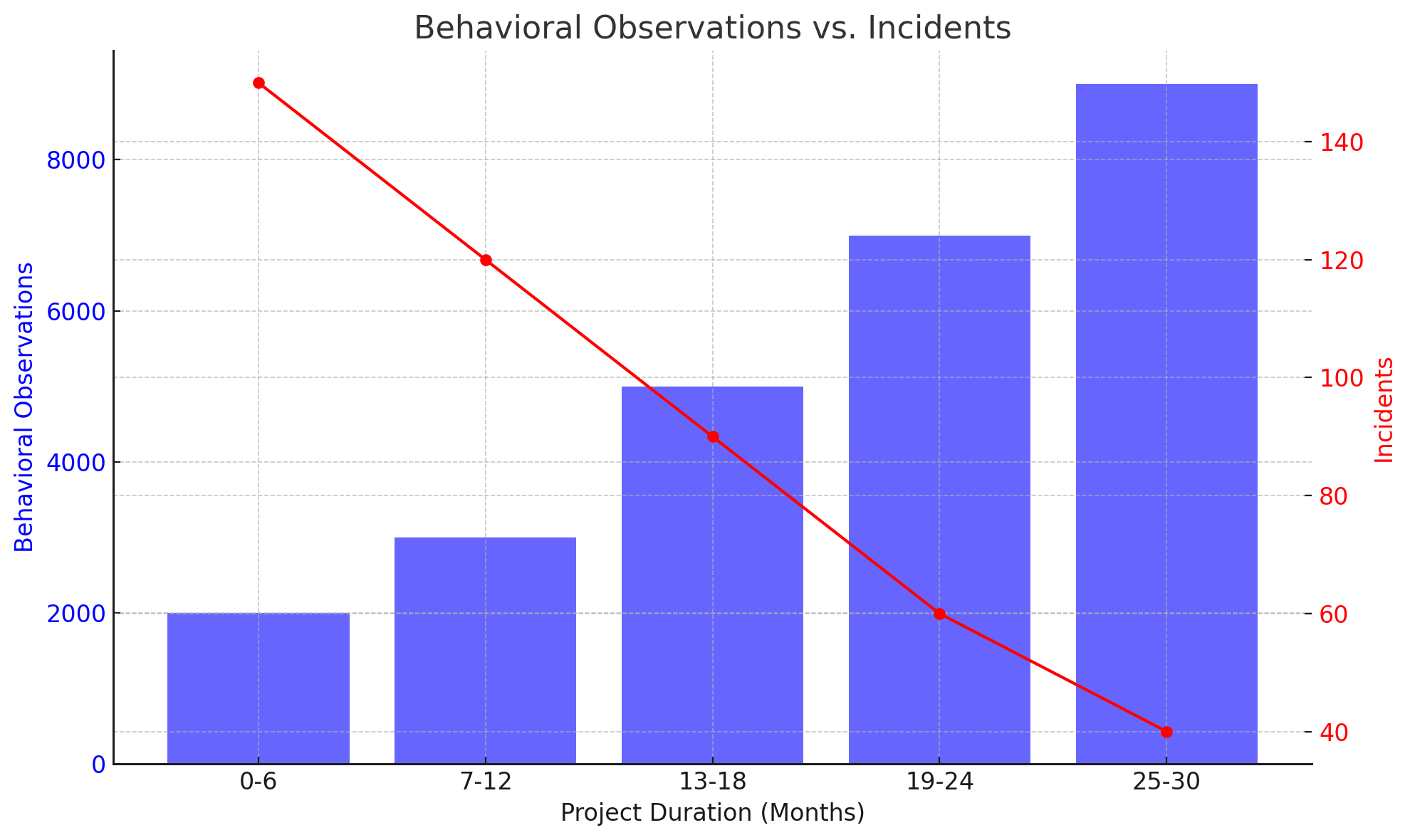
Phase 6 - Data Analytics & Tools (Ongoing)
A key aspect of the project’s success was the integration of a data analytics tool to provide real-time insights:
- Custom Dashboards: These allowed supervisors to track safety behaviors and incidents in real-time.
- Predictive Analytics: The system identified high-risk behaviors before they led to incidents.
- Data-Driven Decisions: Decisions such as increasing safety audits during peak production times were made based on the data analytics provided.
Data Driven Decision : Phase 6
Predictive analytics helped avoid potential incidents by identifying behavior patterns linked to equipment misuse.
BBS Consulting Project Outcome & Results
The BBS implementation yielded significant improvements in the client’s safety culture. Below are the key metrics which demonstrating the project success.
Safety Incident Reduction
60% decrease in safety incidents across all plants.
Near-Miss Reporting
200% increase in reporting, highlighting proactive safety measures.
Behavioral Compliance
98% compliance rate with new safety protocols.
The successful implementation of the Behavior-Based Safety (BBS) program within the steel industry led to substantial improvements in safety practices, a significant reduction in incidents, and an empowered workforce. The integration of data-driven tools enabled real-time monitoring and long-term sustainability of the program.
The project serves as a benchmark for industries seeking to improve their safety standards through behavioral interventions.
Join us and make your company a better place.