How are you developing process safety indicators?
Risk Based Process Safety Management Performance Indicators
The process industry has a long history of major incidents that are well publicised with many valuable lessons to be learned. It has been recognised that the focus on personal safety is one side of preventing accidents. The underlying causes of major incidents are often related to failures in what is commonly known as ‘process safety management’.
As with any aspect of management systems, it is important to have metrics in place to understand how effectively a system is working to its effectiveness.
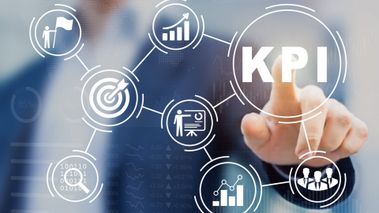
Developing RBPSM Performance Indicators
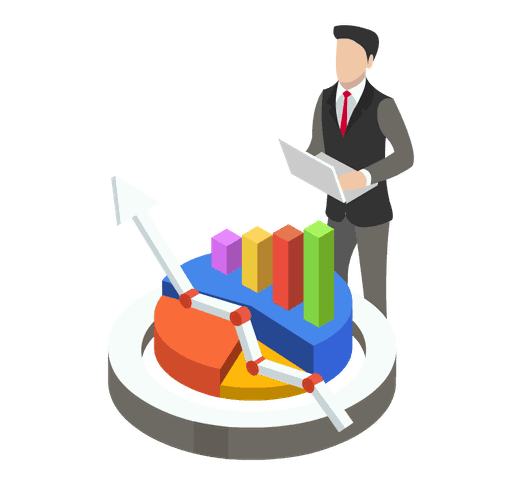
RBPSM PIs should ideally be derived from a rigorous process that identifies the key major accident hazards and uses the accident trajectory analysis to work out the likely causes and associated control measures.
Organisations can use a bow-tie analysis and layers of protection analysis (LOPA) to gain insight into their risk exposures.
Selecting RBPSM Performance Indicators
Selecting RBPSM PIs should consider the risk control system and identify leading (those that are evident before the incident occurs) and lagging indicators (those that are evident after the incident occurs).
RBPSM PIs example to derived are -
Observation trend of hazards as per worksites
Review of the site safety non-compliance cases
Analysis of the incident and accident trends
Learning from external incidents
Corporate Plan for RBPSM Performance Indicators
RBPSM PIs should be part of the corporate strategy to reduce exposure to major accident hazards. In well-developed corporate systems there are common standards and definitions used to set and monitor site and business
sector RBPSM PIs.
RBPSM PIs can be separated into leading and lagging indicators; leading indicators being those that precede a failure of the process safety management system and lagging indicators being those that follow a failure of the process safety management system.
For example, a measurement of the completion of pressure safety valve (PSV) testing would be a leading indicator and the number of times PSVs fail to lift at the set pressure (in use or during testing) would be a corresponding lagging indicator.
Conclusion
PSPIs for the site should be owned by the site leadership team and accountability for the input should be delegated to the various departments and plant area teams. It is recommended that a senior management team member acts as a ‘champion for RBPSM PIs’ during their development.
Corporate and site annual objectives and five- year plans should include RBPSM PI targets (current and next year) and aspirations (five-year horizon).
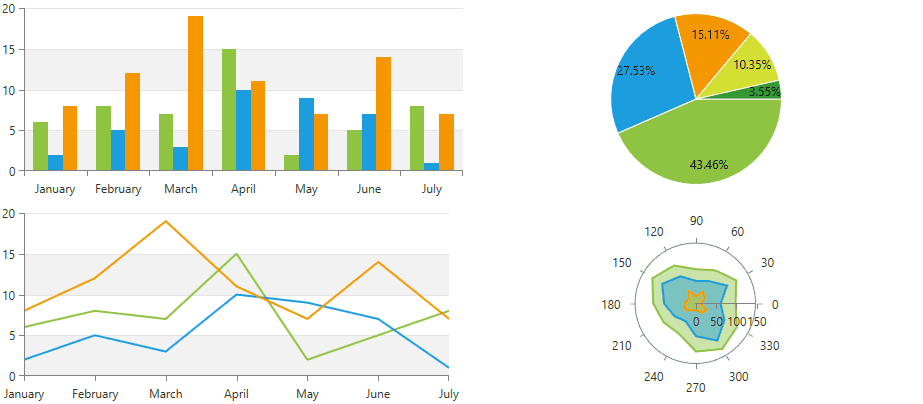